Conducting Levelized Production in a Lean Environment
Editor's Note: This post was originally published in September 2016 and has been updated for freshness, accuracy, and comprehensiveness.
To reduce costs, many manufacturing companies build orders only to keep up with customer demand – but there’s a fine line between waiting too long to begin fulfilling orders (resulting in unhappy customers) and overproducing (creating an unwanted surplus). Levelized production is a lean concept that encourages producing the same amount of product each day; it works best in manufacturing environments that are reasonably predictable.
To accomplish levelized production, obtaining historical trends and utilizing forecasting tools from your ERP system is mandatory; understanding the information is even more critical – using it correctly will create balance and eliminate over/under production.
Say, for example, that you receive 60 widget orders in a week: 30 on Monday, 10 on Wednesday, and 20 on Friday. Using the order history and forecasting tools on your ERP, you could have reasonably anticipated this and built 12 widgets per day for a week. That rate of production – 12 per day – is level and in sync with demand. Proper ERP tools like lead times, scrap factors, bills of material, inventory positions, etc. can help you understand realistic numbers, establish sound “levels,” and manage business better.
Here are just a few benefits of levelized production:
Reduced Labor Costs – Simpler Goals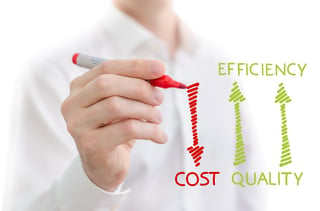
When you face spikes in production demand, you may need to create additional work shifts, pay overtime, or hire contract workers to meet that demand. If you use levelized production, however, a spike in demand wouldn’t faze you – you’d maintain steadier labor costs and keep the expectations of production workers, schedulers, and supervisors under control.
Clearer Inventory Position
Predicting how much inventory is, or will be, on hand clarifies the requirements of your production personnel and establishes financial expectations, as the cost of carrying inventory is understood and minimized.
Improved Quality Control
In the event of a quality problem, levelized production means that you'll immediately know the impact on the affected units. A non-levelized approach, however, means that a large batch was built and stored for a longer period; when you unearth the root of the quality problem, it’s harder to determine the cause as well as much costlier.
Improved Customer Service
Levelized production prevents capacity from being fully booked and/or overbooked, increasing your responsiveness to special requests or fulfilling large orders on time, resulting in better happier customers.
Are you interested in using an ERP system in a lean environment to feed a levelized production approach? If so, the experts at Acuity would love to hear more about your production planning processes and help you implement a strategy tailored to your business! Contact us today for more information.