Every 5 years, a committee reviews ISO standards to establish whether or not they're relevant in the current market. If they're not, they're revised to maintain relevance; ISO 9001:2015 was revised to respond to the latest trends and to achieve compatibility with other management systems, such as ISO 14001. And although the revisions are always made with the same goal in mind, the changes made during the ISO 9001:2015 revision are considerably more significant than those made in the 2008 revision.
Let’s take a look at some of the reasons for these updates:
Leadership Responsibilities
A commitment to quality through strong, visible leadership has been reinforced in ISO 9001:2015, placing requirements on top management (who direct and control the organization at the highest level) versus individuals and/or management representatives responsible for the QMS. Top management must also ensure that requirements are properly integrated into business processes and that they are compatible with the strategic direction of the organization.
Action Planning
There is now an increased focus on the creation of actions to address risks and opportunities as well as the integration and implementation of those actions into management system processes. Actions must be monitored, managed, and communicated across the organization for a better evaluation of their effectiveness.
Supporting Documents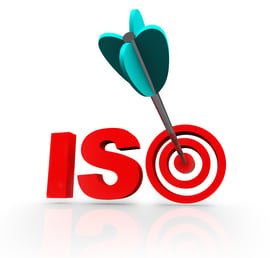
Organizational knowledge is a new requirement that addresses requirements for aptitude, awareness, and communication of the QMS. Employees must be aware of the quality policy, recognize their contribution to it, and understand the implications of nonconformance.
In addition, there are now requirements for “documented information” – a new term that replaces the "documents" and "records" in the 2008 standard – and it is the responsibility of the organization to determine the level of documented information necessary to control the QMS.
Operational Standards
There is now greater emphasis placed on the control of processes – particularly planned changes, the review of consequences produced by unintended changes, and/or qualifying adverse effects where necessary. Revisions to this category also acknowledge trends in the increased use of subcontractors and outsourcing and the need for performance monitoring.
Performance Evaluation
An emphasis on the need to understand customer views and perceptions with regards to a particular organization now exists. Organizations must provide analysis and evaluation of this data and how they use it for QMS improvements.
Opportunities for Improvement
Organizations are now required to actively seek out opportunities to improve processes, products and services, and the QMS. This new requirement for continuous improvement has also been extended to cover the adequacy and effectiveness of the QMS, but does not specify how an organization should achieve this (That is, each organization gets to choose how to meet this requirement.)
While these changes may seem time consuming and challenging, they provide an opportunity to review your current approaches and make adjustments where necessary to keep your business running as efficiently as possible. Ultimately, these standards are designed to help your business grow, improve customer satisfaction, and increase profitability.
Are your systems set up to manage ISO compliance? Are you taking advantage of newer ERP system capabilities? The experts at Acuity would love to hear more about your ISO efforts and explain our supporting systems to improve your business. Contact us today for more information.